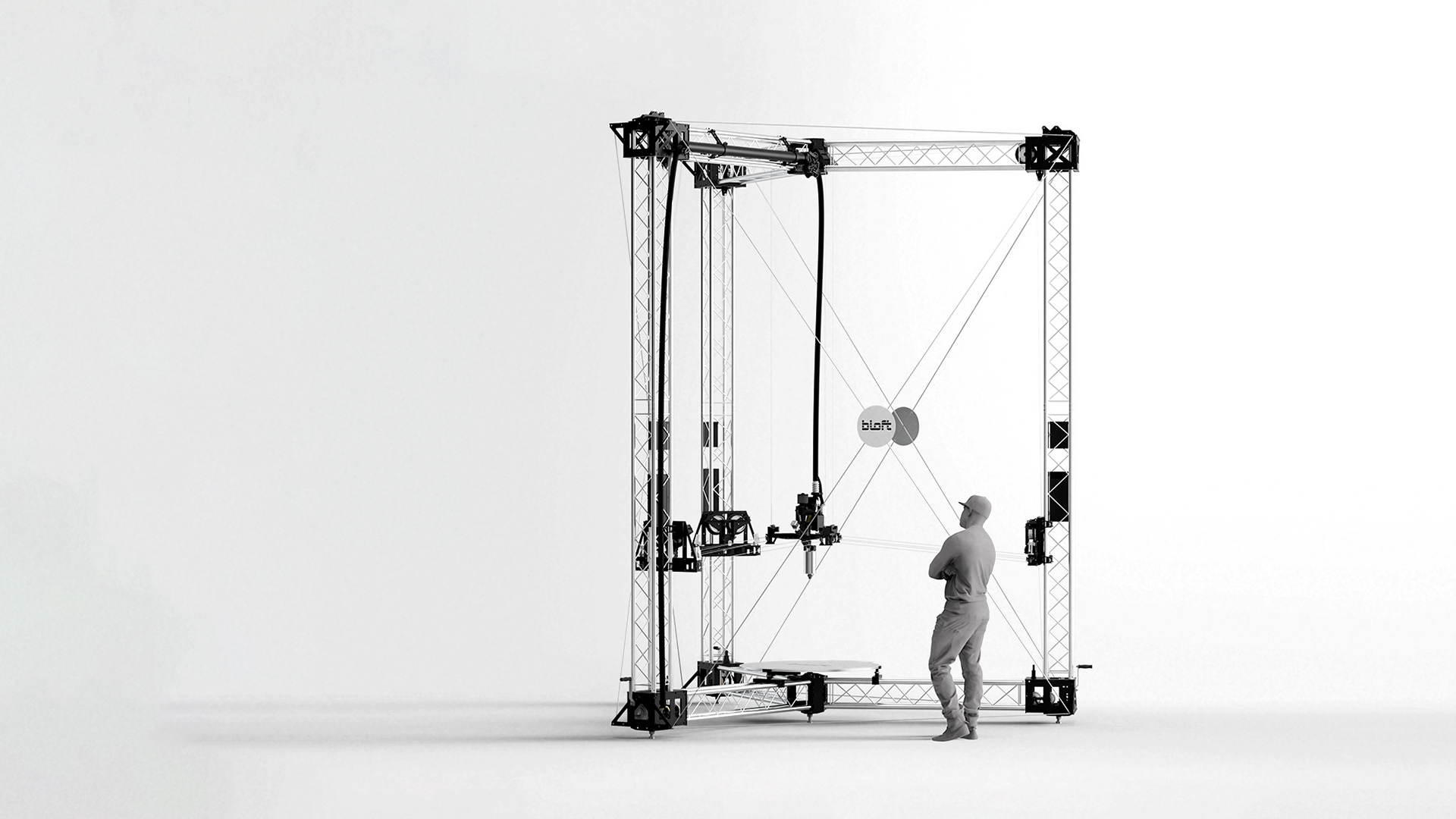
The need for a more rigid printer frame was the initial design driver, but based on the operational insight from the first printer there were also other design drivers. Since the main benefit of the cable-driven motion system is it's unbeatable size-to-cost factor, there was a need to ensure this benefit could be exploited as good as possible. Hence, modularity was defined as the second design driver. In the spirit of open source the manufacturing methods, materials and components had to be chosen with a low entry threshold in mind. A light weight and modular truss system, commonly used for rigging, was chosen as the structural backbone of the printer.
Furthermore, I wanted to enhance the print volume limitations of the first printer iteration. This was caused by fixed mounting points of the horizontally oriented lines, which effectively limited the width of the printed object the taller the object was. The solution to this problem were mounting point traversal along the Z-axis or simply along the vertical trusses. This made it possible to print objects up to 2-2.5 m height with the current frame setup. The print bed had a diameter of 1 m.
Since we wanted to enable printing without supervision, it meant we had to develop a solution for transporting the printing material, either plastic pellets or shredded plastic flakes, to the print head. As solution we decided to go with a flexible plastic hose, which runs parallel with the power and signal lines to the print head. The other end is attached to a plastic granulate dryer, which keeps moisture off the plastic improving the overall print quality.
The printer is operational since May 2021 and it has been used in several pilot projects to test 3D printability of plastic waste. The concept was awarded with the 2nd place at the Hackaday Prize 2022.
Bloft Mk2 Specifications
Dimensions ca. 4.5 x 4.5 meters, weight ca. 350 kg
Print volume dimensions ca. 1000 x 2500 mm (cylindrical)
Motion system travel speeds up to 1800 mm/sec in XY-plane
Extruder throughput up to 500 mm3/sec
Extruder temperature up to 300 degree C
Bed temperature up to 100 degree C
Print volume dimensions ca. 1000 x 2500 mm (cylindrical)
Motion system travel speeds up to 1800 mm/sec in XY-plane
Extruder throughput up to 500 mm3/sec
Extruder temperature up to 300 degree C
Bed temperature up to 100 degree C
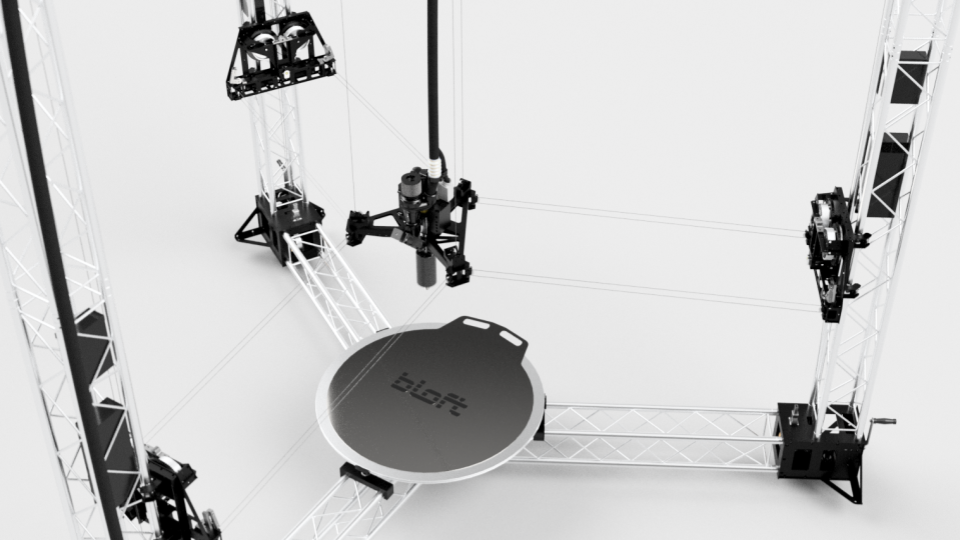
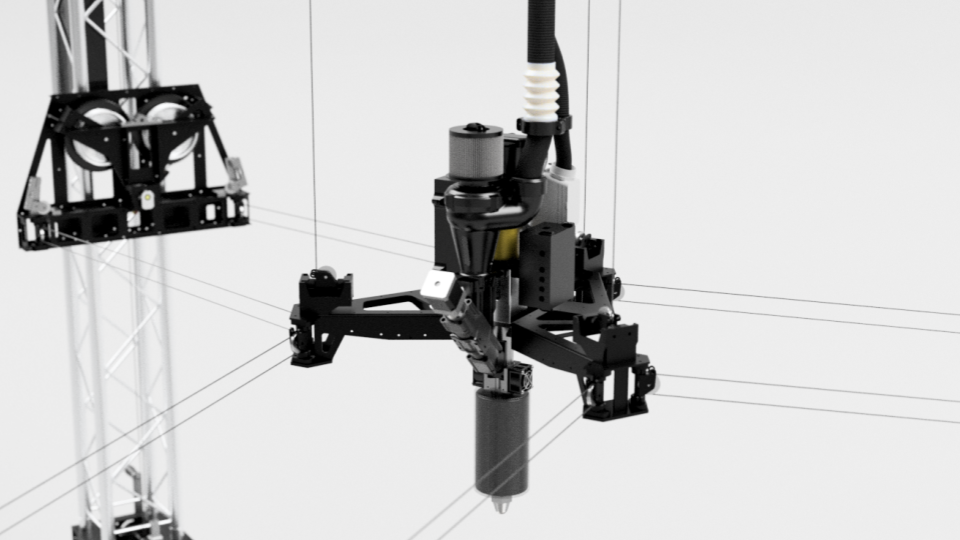
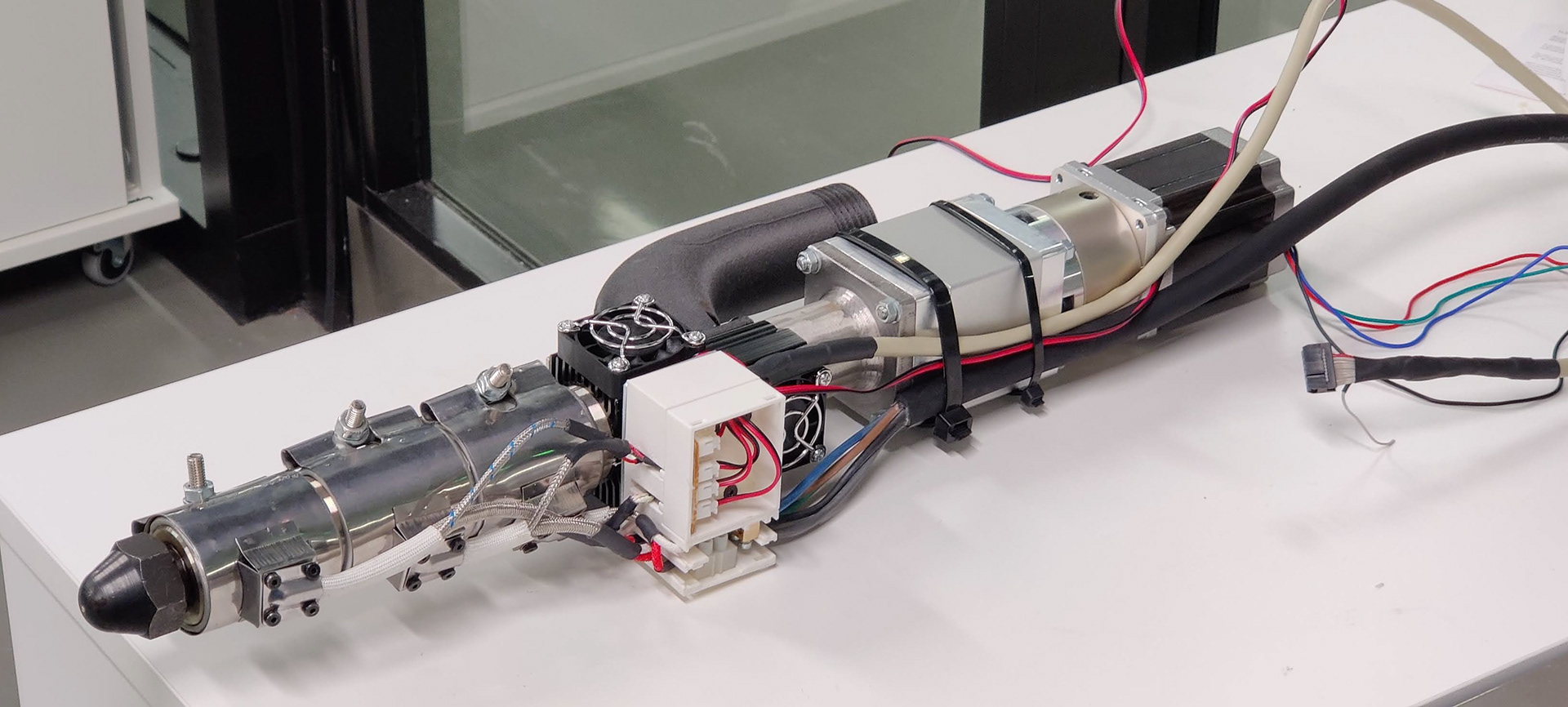
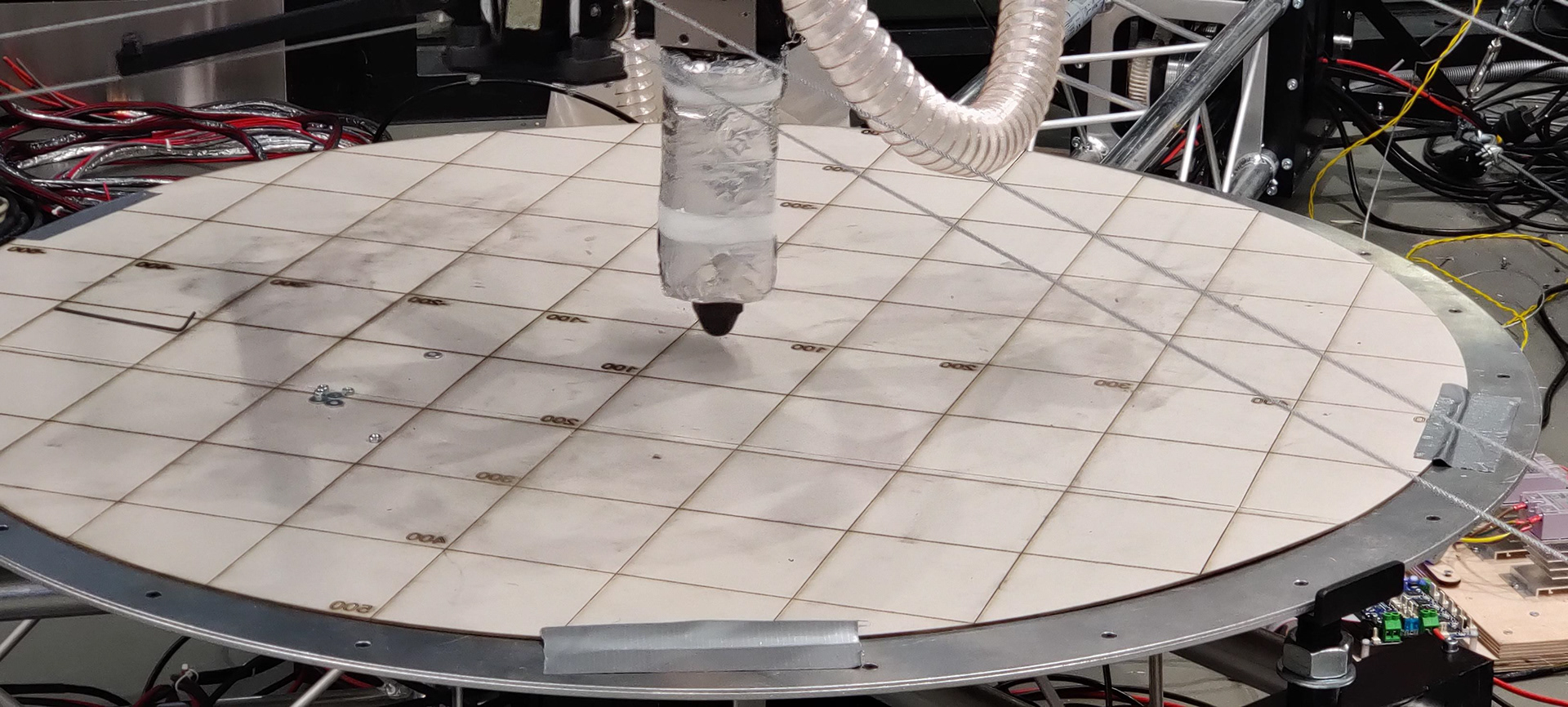
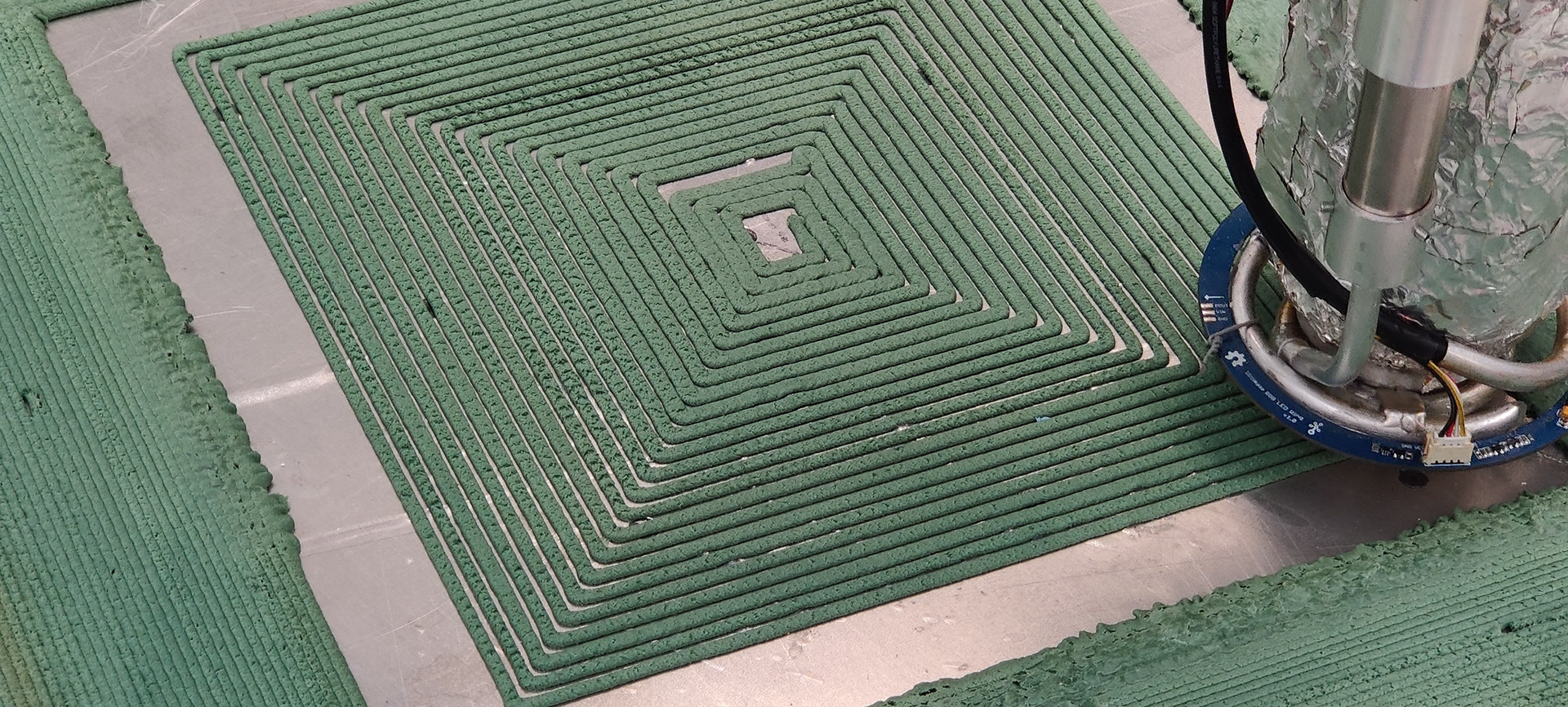
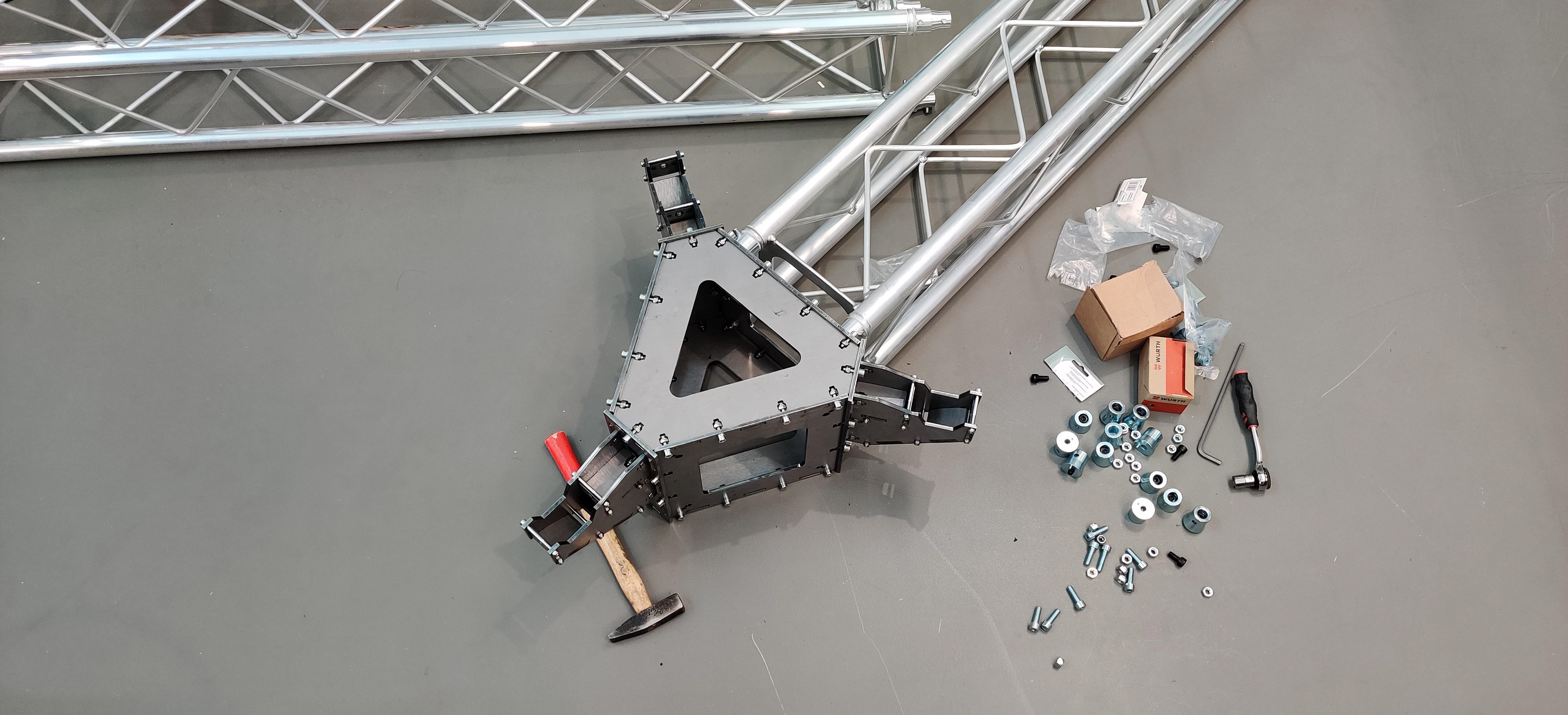
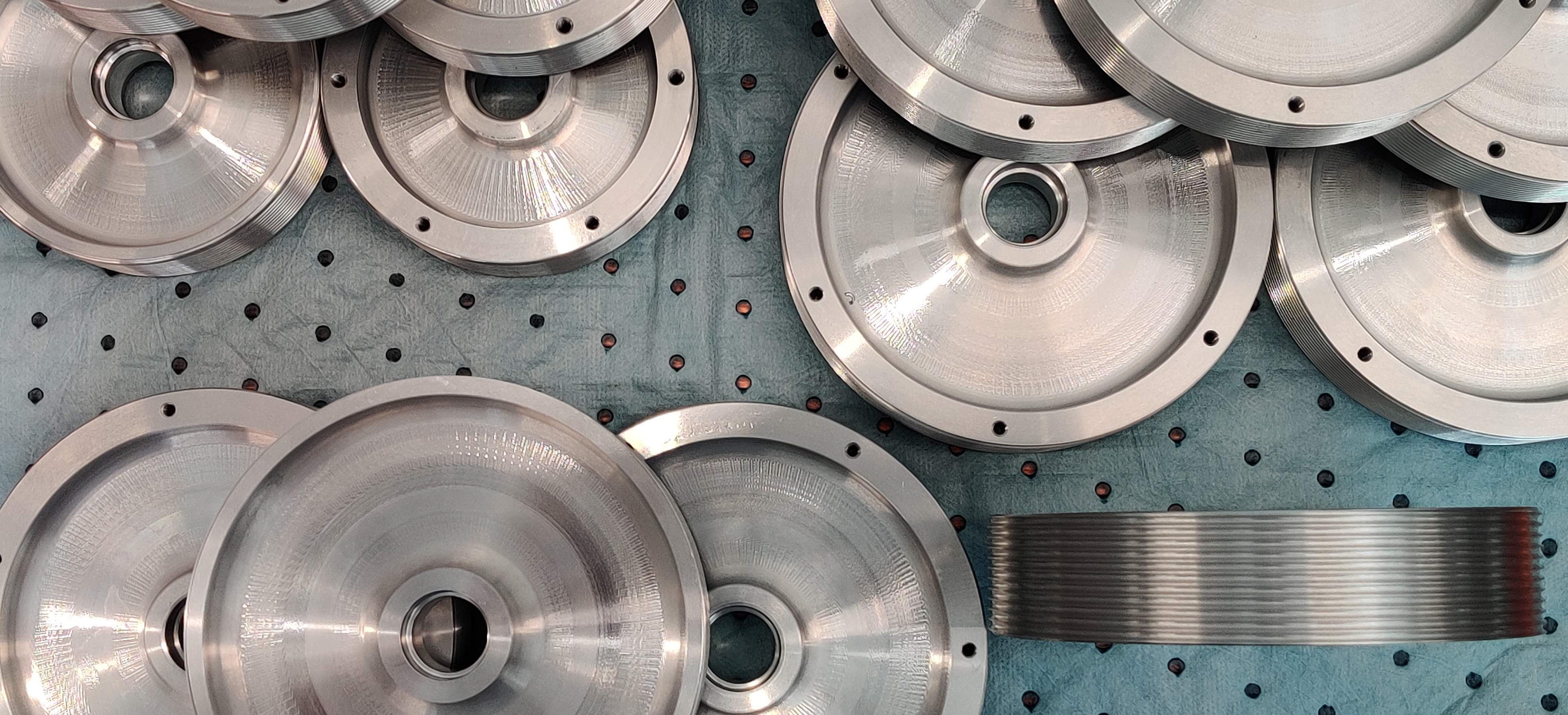
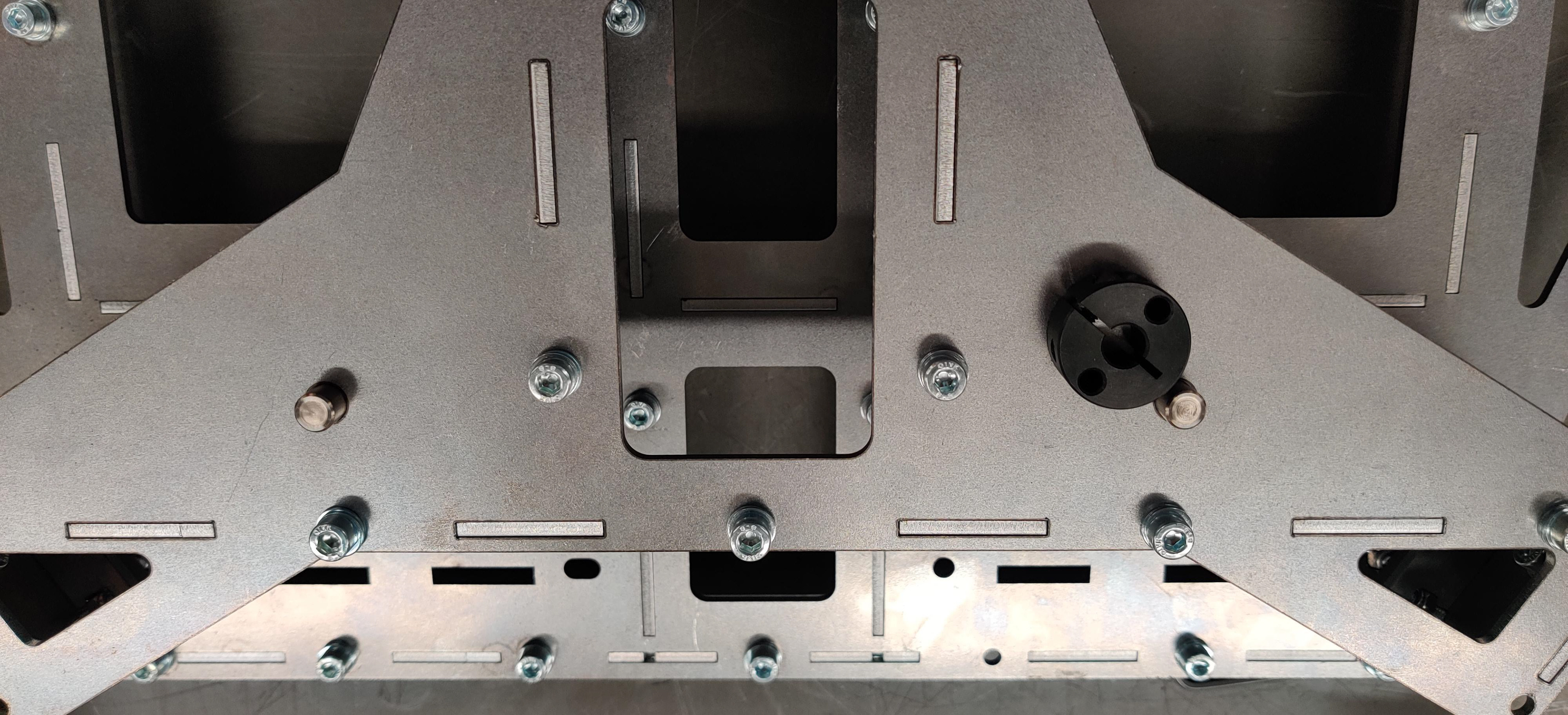
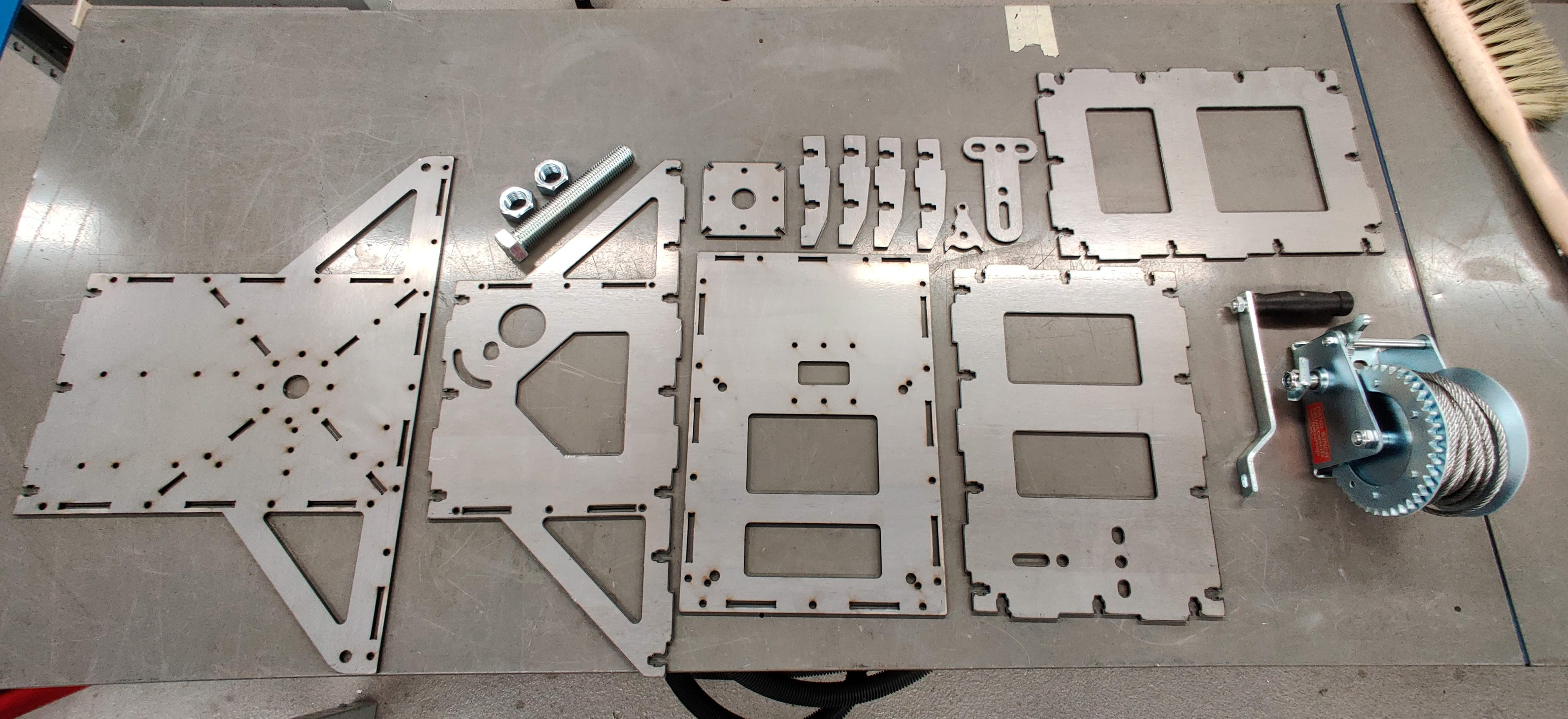
Some details on the build process and individual parts of the frame.
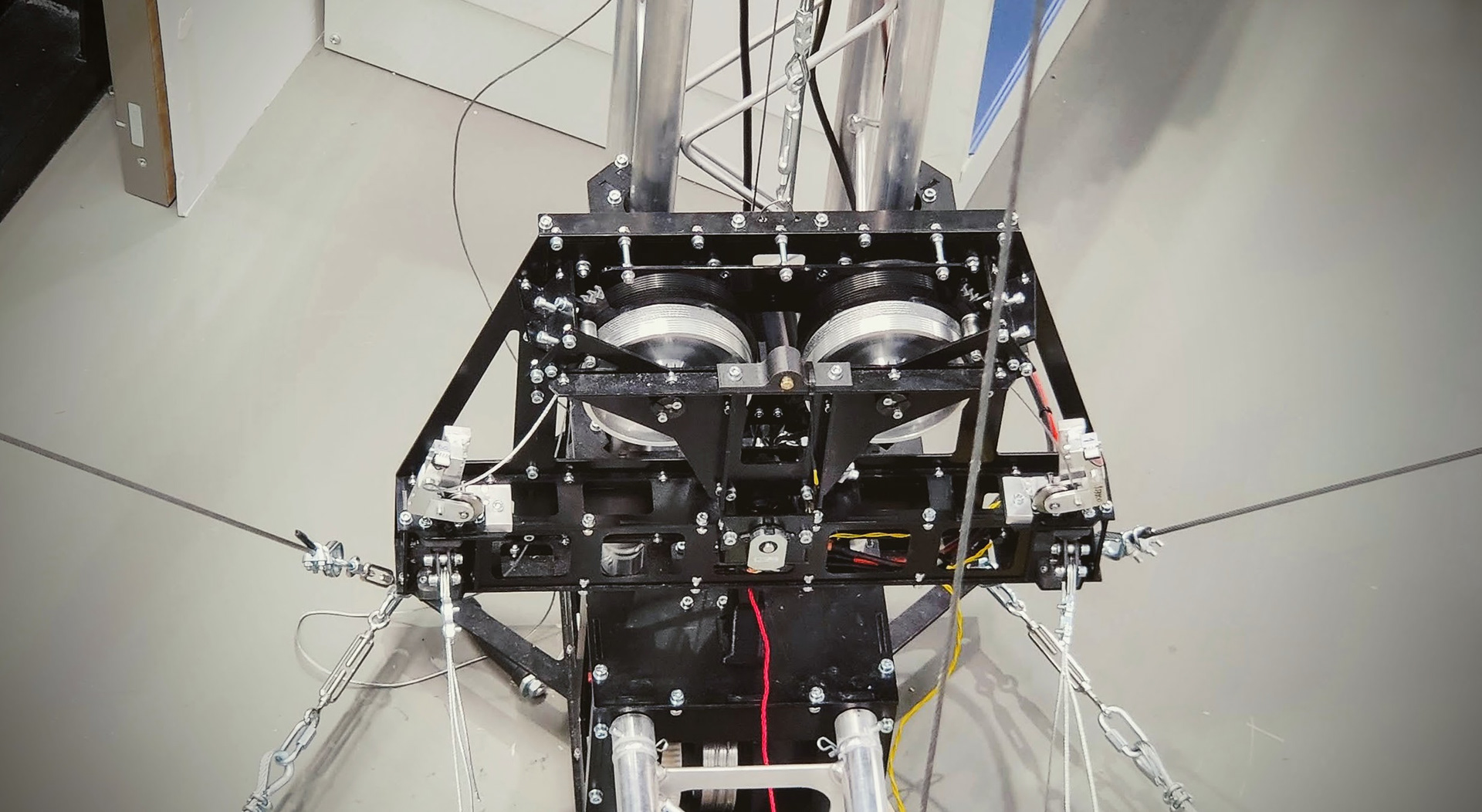
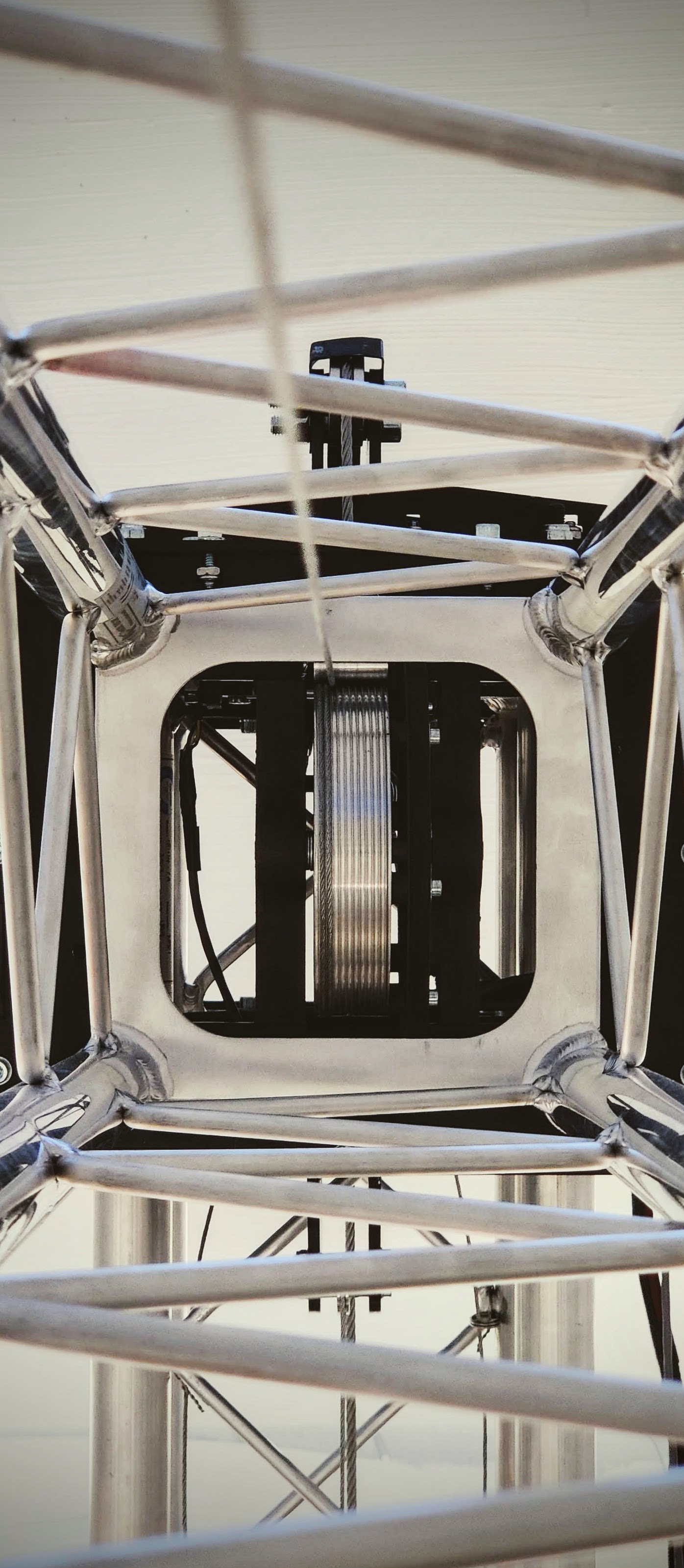
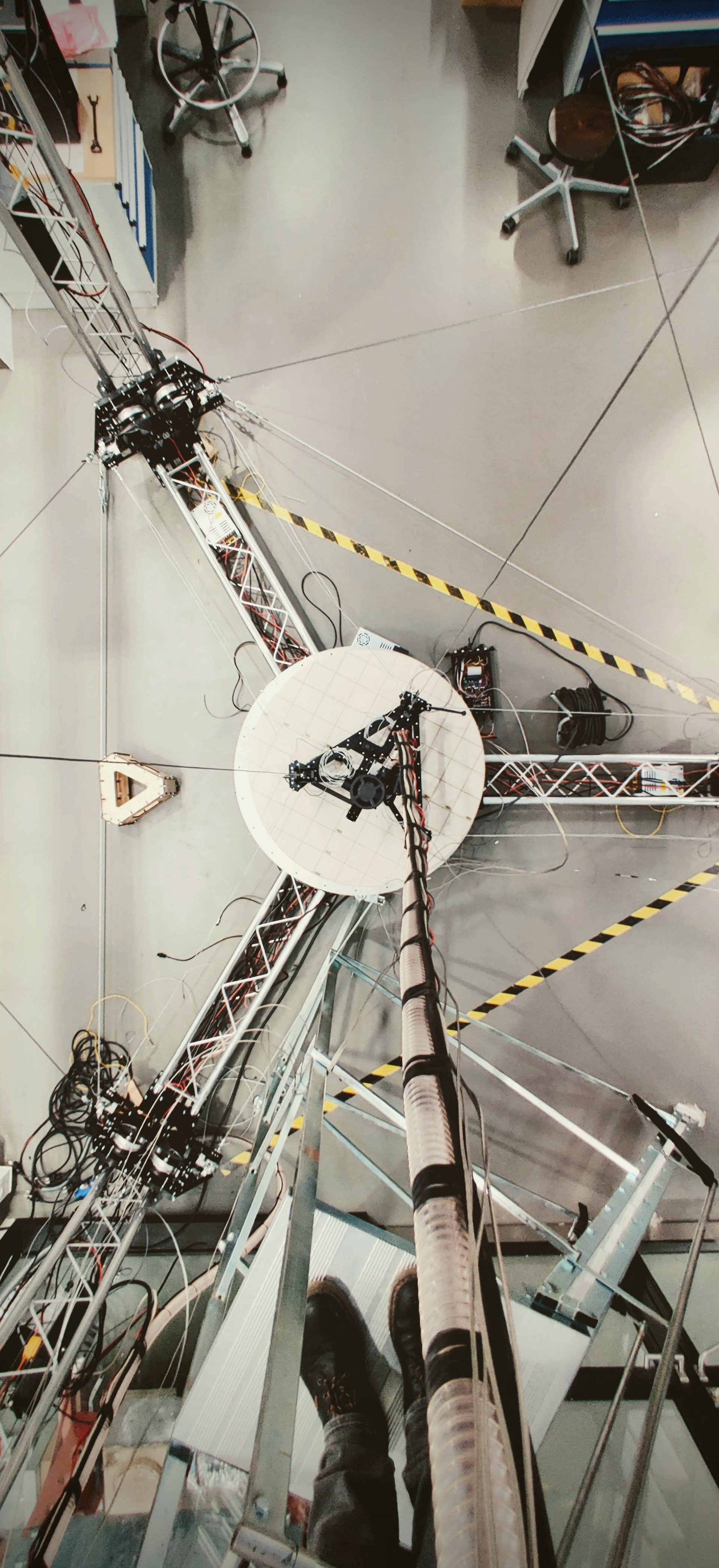
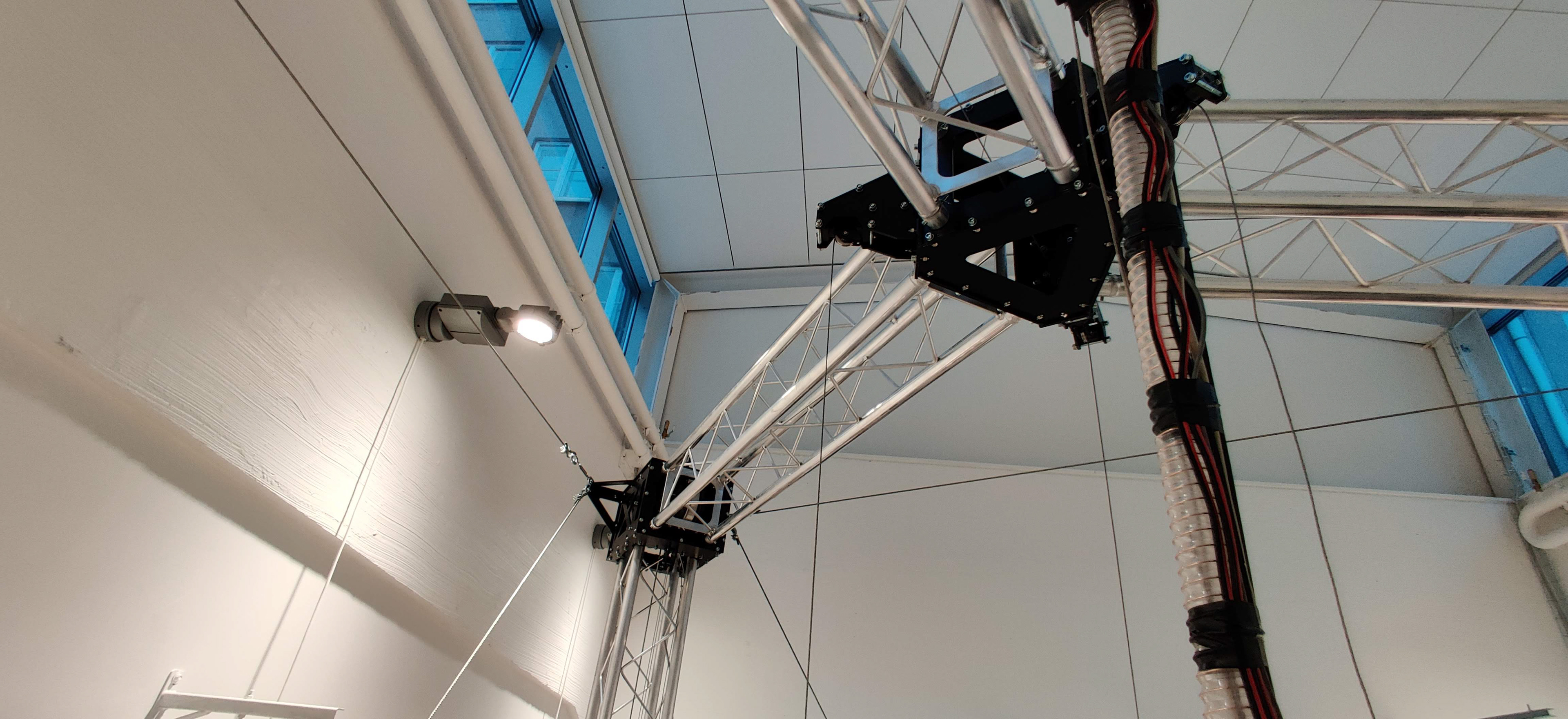
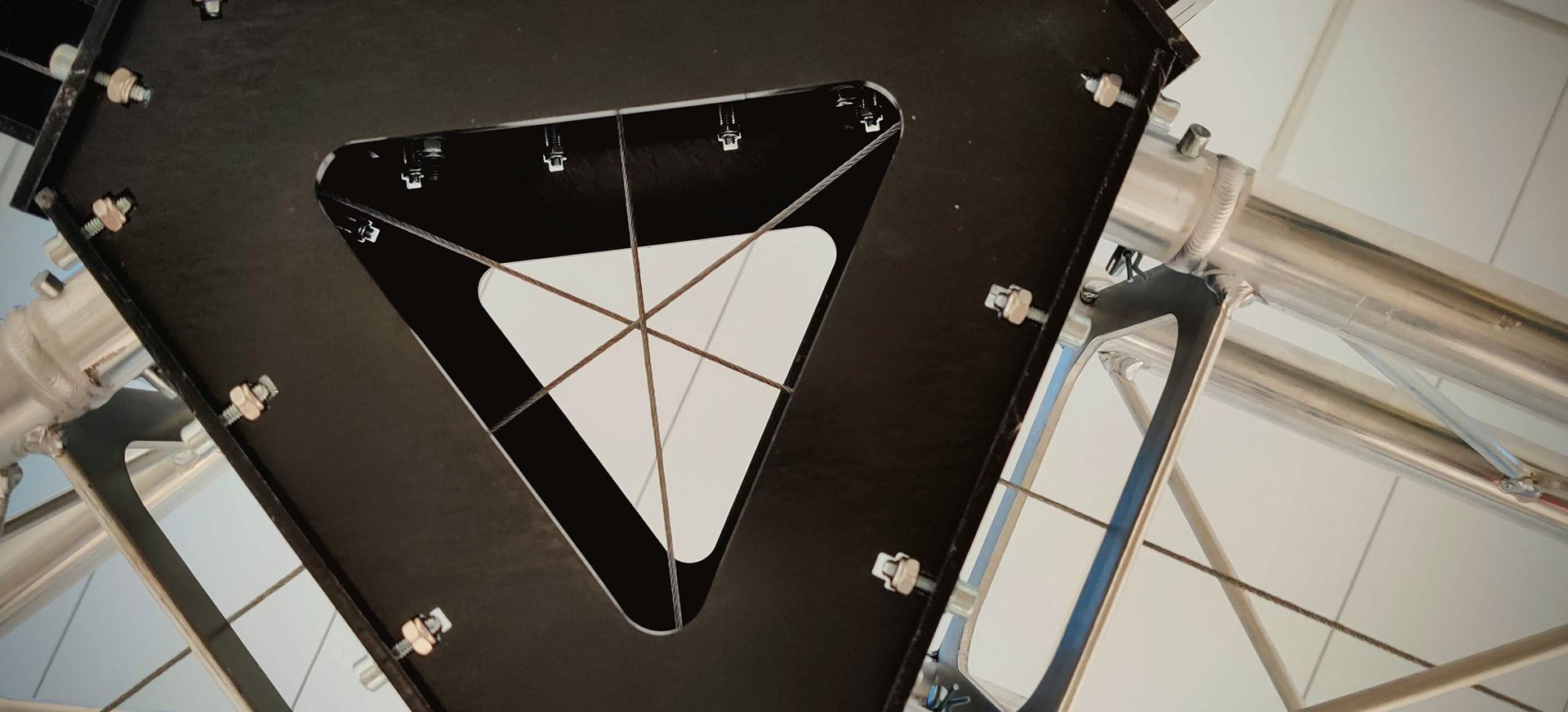
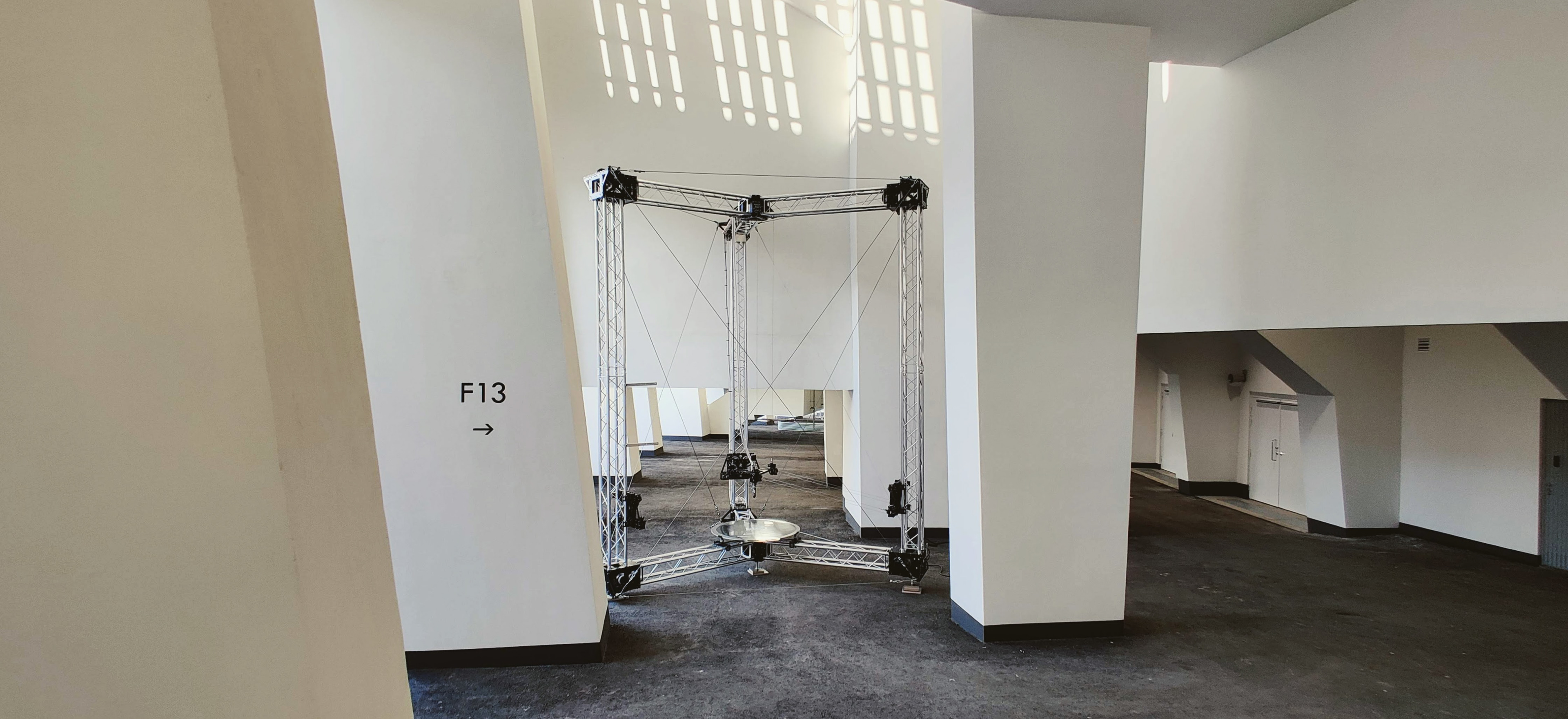